
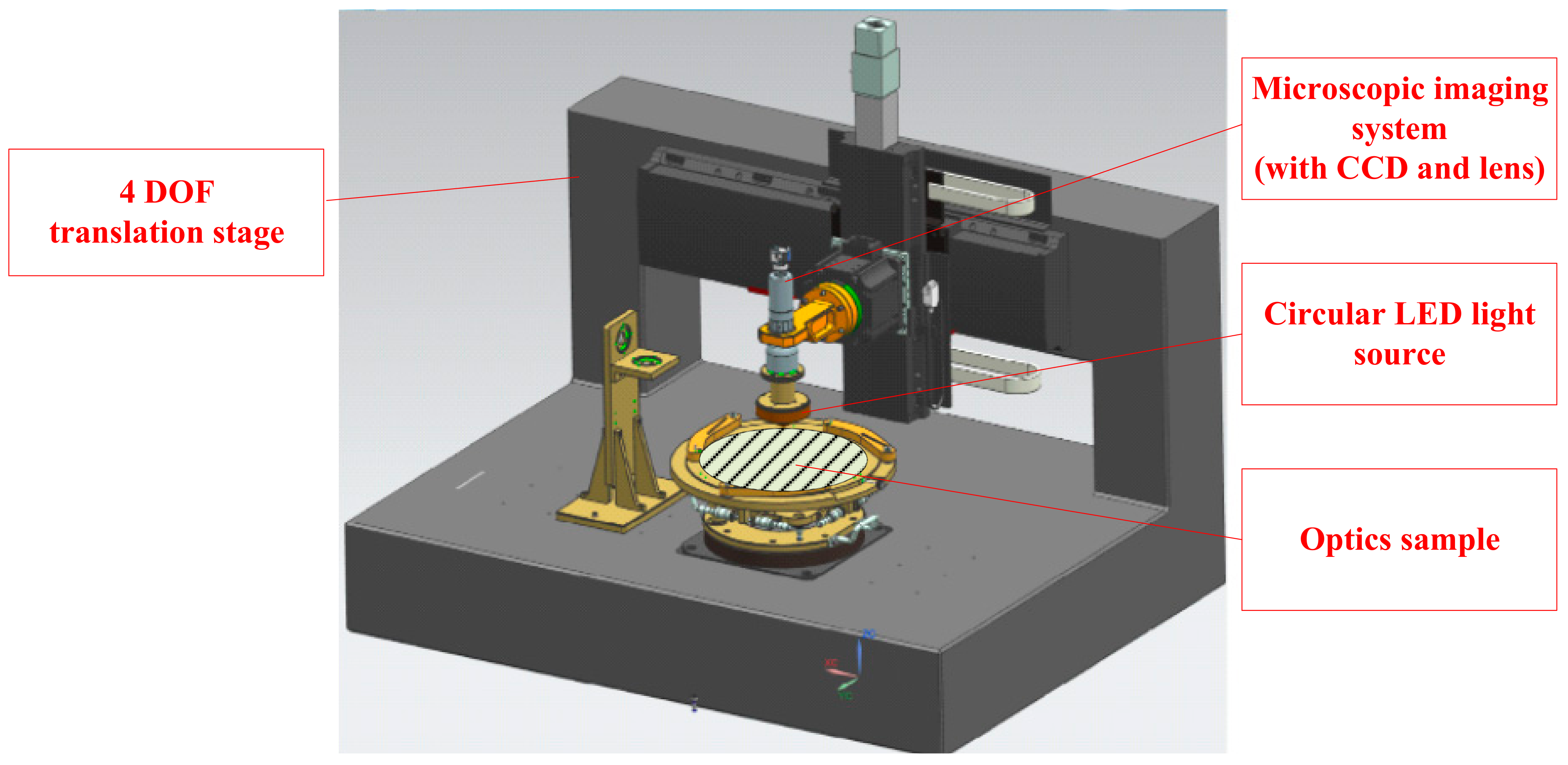
Once all the scratches and digs on an optical filter are classified, MIL-PRF-13830B lists further requirements for the scratches and digs that fall into the maximum allowable category as determined by the specification. For example, a common scratch-dig specification of 60-40 means that no scratches can appear wider than the ‘60’ comparison standard and no digs can have a diameter larger than 0.4 mm.
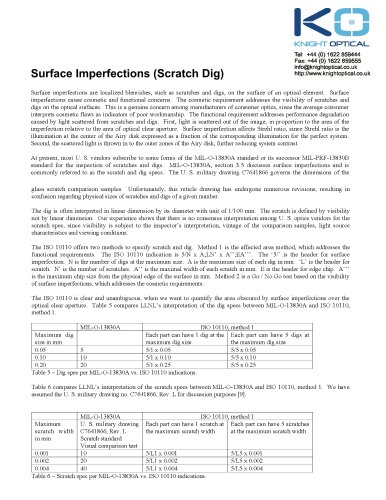
While the dig value roughly corresponds to the diameter of the imperfection, the scratch value only refers to the apparent width of the scratch when compared to the standard. In the case of MIL-PRF-13830B, evaluation is performed by visual comparison between the imperfections on an optical filter and a reference part using specific lighting conditions outlined in the document. Most military and ANSI standards call out scratch-dig surface quality specifications as a set of numbers that correspond to the respective size of the scratch or dig. Definitions, evaluation methods, and evaluation time can all vary depending on which standard is used. Surface quality specifications are typically called out according to a set of standards defined by the United States Military, the American National Standards Institute (ANSI), or the International Organization for Standardization (ISO). Although some surface imperfections are purely cosmetic, many can introduce unwanted scattering or make the optical filter more susceptible to laser induced damage, resulting in decreased system performance. Surface quality specifications refer to the type and amount of allowable imperfections on each of the coated or uncoated surfaces of an optical component. Custom and OEM Optical Filter Development.
#Iso 10110 scratch dig series

Stress birefringence in accordance with ISO 10110-2 (nm/cm)īubbles and inclusions in accordance with ISO 10110-3 Range of maximum (diagonal) dimension of part Table of permissible deviations and material imperfections in case these parameters are not given: “Rq 0.05-2 G√ 5” indicates a ground surface with Rq between 0.05 – 2 microns with minimum sample length of 5mm. Often you might see a polished surface classified as: LN”xA” = number of allowed long scratches where A” is the maximum allowed width of scratches over 2mm, expressed in mmĮA’’’ = edge chips where A’’’ is the maximum inward extent of the chip in mm NxA = number of allowed surface imperfections where A is the square root of the area of maximum allowed imperfection in mmĬN’xA’ = number of allowed coating blemishes of maximum size where A is the leg length of a sample square in mm “4/ σ” defined as the maximum tilt angle at the datum axis in minutes (‘) or seconds (“) of arc. 2/ 1 2)Ī = maximum power deviation (peak to valley) from a test plate in fringe spacingsī = maximum value of irregularity (peak to valley) in fringe spacingsĬ = maximum value (peak to valley) of rotationally symmetric irregularity in fringe spacings (rarely used)

Both parameters are categorized in terms of a class. "2/ A B" Inhomogeneity is a gradual variation of index within an element. Striae is the term for inhomogeneities having a small spatial extent. “1/ NxA” where N is the number of bubbles or inclusions of maximum permitted size in the material, and A is the measure of their size in mm, equal to the square root of the projected area of the largest permissible bubble and/or inclusion in mm. “0/ A” where A is the maximum allowable stress in nm/cm of optical path length in the sample material.
